DIGITALISIERUNG DER FOOD-PRODUKTION
Von der Automatisierung zum Informationsmanagement - was heute in der Food-Produktion zählt:
Die Digitalisierung der Prozesse.
Finden Sie sich in einer dieser Aussagen wieder?
Das Warenwirtschaftssystem ist noch nicht richtig mit der Produktion vernetzt. Dies ist eine der Grundaufgaben eines Fertigungsmanagementsystems (MES). Produktionsaufträge werden (ungeordnet) zusammen mit Informationen über Rohstoffe und Hilfsstoffe wie Verpackungsmaterial vom Warenwirtschaftssystem an das MES übertragen. Produzierte Mengen und Rohstoffverbräuche werden in Verbindung mit Chargeninformationen zurückgemeldet sowie ggf. auch Statusinformationen über den aktuellen Verlauf der Produktionsprozesse.
Prozessschritte, die auf Laufzetteln dokumentiert werden, sollten direkt vom MES geführt und dokumentiert werden. Dies kann auch mit Hilfe von mobilen Endgeräten (mobile devices), wie z. B. Barcode bzw. QR-Code-Scannern erfolgen und durch den Einsatz von Industrie-PC’s in hygienischem Design direkt auf dem Shop Floor bzw. an den Maschinen / Linien.
Der Vorteil: Informationsmanagement wird möglich oder in anderen Worten: Alle Daten sind in Echtzeit an jedem Endgerät verfügbar (die entsprechende Nutzerberechtigung vorausgesetzt). Fragen nach dem Verbleib eines Laufzettels oder der aktuellen Version einer Exceltabelle sind Geschichte. Das MES führt alle materialwirtschaftlichen Aspekte und Buchungen aus dem Warenwirtschaftssystem in der Produktion konsequent weiter. Rohstoffe, Halbfabrikate und Produkte werden chargengenau gebucht. Für Mischchargen wird eine neue Chargennummer angelegt, sodass jederzeit die Auflösung einer Mischcharge mengengenau und nach vorgegebener Konzentration möglich ist. Auch Ereignisse, die nicht direkt chargenrelevant sind, wie z. B. Audits, werden natürlich konsequent dokumentiert.
Für die Intralogistik gilt dies ab / bis Werkstor einschließlich Steuerung der LKW-Verkehre am Standort mit Hilfe von Selbstbedienterminals („Hofmanagement“), also deutlich über die Grenzen der Produktion hinaus.
Verschiedene Premixe oder Halbfabrikate werden an unterschiedlichen Orten vorproduziert und müssen über Transportbehälter oder Palettenware der Produktion (z. B. an Mischern oder Prozessbehältern) zur Verfügung gestellt werden.
Bei der Herstellung der Premixe bzw. Vorprodukte ist bereits die Auswahl der korrekten Rohstoffe durch den Einsatz von Scannern zu überwachen und die Chargenverwendung im Fertigungsmanagementsystem (MES) zu dokumentieren. Hierbei werden auch die Transportbehälter bzw. Transportgebinde mit Scannern (oder RFID-Tags) identifiziert und dem Teilauftrag zugeordnet. Vor der Zugabe in den nachfolgenden Prozess, z. B. in einen Mischer, wird der Transportbehälter wieder identifiziert. Es erfolgt die Prüfung auf Richtigkeit der Zugabe gemäß Rezept und die chargengenaue Dokumentation der zugeführten Rohstoffchargen. Gleichzeitig wird auch der Status der Transportbehälter überwacht, sofern diese mehrfach verwendet werden. Somit lassen sich Reinigungszyklen definieren und sicherstellen sowie das Allergen-Handling wirksam überwachen.
Am Ende der Produktionskette kann die Chargeninformation der Produktionscharge automatisiert an die Verpackungsmaschine übergeben werden, sodass aus dem Verpackungsaufdruck eindeutig auf den gesamten Produktionsprozess und die verwendeten Rohstoffe rückgeschlossen werden kann. Das Chargenprotokoll umfasst hierbei ausdrücklich nicht nur Rohstoffdaten, sondern auch beliebige weitere Verarbeitungsinformationen wie Maschinenparameter, Identifikation der beteiligten Werker und sämtliche Produktionszeiten der einzelnen Prozesse. Dies schließt auch die Verfolgung des MHD mit ein sowie ggf. die Überwachung von Verpackungsmaterial und Produktkennzeichnung.
Sollte nach einer Reklamation z. B. durch Rückstellmuster ein Qualitätsmangel einer Rohstoffcharge oder eines Halbfertigproduktes identifiziert werden, so erlaubt die Tracking-Funktion des MES die Identifikation sämtlicher Fertigprodukte, in denen die auffällige Charge verwendet wurde. Ein begrenzter, ggf. stiller Rückruf wird somit vom MES ermöglicht.
Kundenindividuelle Aufträge erfordern Rüstzeiten für Maschinenparameter, Maschinenwerkzeuge sowie Verpackungsmaterial und Etikettierung. Gleiches gilt für kurzfristige Nachbestellungen.
Das Zusammenfassen von vielen Kleinaufträgen zu einem größeren Produktionsauftrag vermindert die Rüstzeiten, muss jedoch organisiert werden. Gleiches gilt für eine Planung der Produktionsreihenfolge mit möglichst wenig Rüstschritten. Hier unterstützt ein modernes Fertigungsmanagementsystem (MES) die Arbeitsvorbereitung. Ggf. lohnt der Einsatz eines Feinplanungsmoduls auf Basis von Künstlicher Intelligenz (KI).
Rüstzeiten, die in Verbindung mit Datenmanagement stehen (z. B. Etikettendruck und Maschinenparameter), können durch automatisierte Schnittstellen drastisch verkürzt werden. Lebensmittelverarbeitende Unternehmen übernehmen als Dienstleistung beispielsweise die Aufgaben des LEH zur Preisauszeichnung. Viele Kunden fordern zudem individuelle Angaben oder Schmucketiketten mit Qualitätssiegel sowie Hinweise zur Herkunft. Zur Nachverfolgung der Produkte müssen Chargennummern und mitunter spezielle Rückverfolgbarkeitslösungen wie z. B. fTRACE unterstützt und die Informationen gedruckt werden. Das MES stellt hierbei automatisch die richtigen Daten für den Etikettierer / Preisauszeichner bereit.
Ein Teil der Qualitätsprüfungen lässt sich möglicherweise automatisieren, indem manuelle Prozesse, wie die Parametrierung von Maschinen, automatisiert und somit vom Fertigungsmanagementsystem (MES) verlässlich gesteuert und dokumentiert werden. Manuelle Vorgänge, wie das Einlegen von Tiefziehfolien oder Etiketten, lassen sich vom MES auch auf Plausibilität prüfen: Der Werker scannt beispielsweise den QR-Code des Materials. Dies ist ein verpflichtender Prozessschritt, ohne dessen Ausführung das MES die weitere Produktion nicht freigibt. Eine solche Freigabe kann entweder am Maschinen- / Linien-PC angezeigt werden oder auch per Hardware-Kontakt den Betrieb der Maschine / Linie unterbinden.
Für interne Audits bietet das Fertigungsmanagementsystem (MES) die Steuerung der Prozesse an. Der Verlauf wird entsprechend im System dokumentiert.
Beliebige Prüfwerte können der Charge des Rohstoffs / Halbfabrikats / Produktes beigefügt werden. Eine Verwaltung von Papieren für die QS-Dokumentation ist nicht mehr erforderlich.
Eine weitere Verbesserung der Qualitätssicherung kann mit Hilfe von Künstlicher Intelligenz erzielt werden, indem die fertig gedruckten und geklebten Etiketten mit einem „Machine Vision“-System (Bilderkennung und Verarbeitung) erfasst und auf Plausibilität geprüft werden. Texte und QR- bzw. Barcodes werden online erkannt und in einen Datensatz konvertiert, der wiederum an das MES zur Prüfung gemeldet wird. Systematische Druckprobleme, wie Tintenmangel, verschobener Laserdruck etc. erkennt das System nach einer entsprechende Anlernphase ebenfalls mit einer hohen Erfolgsquote automatisch.
In der Regel werden während der Produktion Qualitätsmerkmale (QCP’s) überwacht. Sobald es sich dabei nicht mehr um einfach zu messende Größen wie Temperaturen oder Gewichte handelt, kommen als smarte Sensoren häufig Kamerasysteme (Machine Vision Systeme) mit einer Software zur KI-gestützten Bildverarbeitung zum Einsatz. Die manuelle Probennahme kann so häufig automatisiert werden und deckt nicht nur einzelne Proben, sondern (fast) die gesamte Produktionsmenge ab.
Der Kunde ist König und verlangt dem Hersteller im Hinblick auf kurzfristige Bestellungen einiges ab. Der Einsatz eines KI-basierten Prognosetools kann die Auftragseingangsvorhersage wesentlich verbessern. Hierbei werden umfangreiche historische Verkaufsdaten mit externen Daten, wie z. B. Ferienzeiten oder Wetterdaten, angereichert und mittels KI-Algorithmen verarbeitet. Das Neuronale Netz ist in der Lage, für den Menschen nicht erkennbare Strukturen und Zusammenhänge in den Daten zu identifizieren und für die Prognose zu nutzen. Das Neuronale Netz ist zudem absolut objektiv und spart wertvolle Zeit für die manuelle Abschätzung des zukünftigen Auftragseingangs bei den Mitarbeitern im Vertrieb.
Und wenn es doch zu unerwarteten Bestellungen oder Bestelländerungen kommt, dann errechnet das Fertigungsmanagementsystem (MES) auf Knopfdruck eine neue optimierte Produktionsreihenfolge. „Optimiert“ bedeutet hierbei die Neuberechnung unter Berücksichtigung von Gütekriterien, die der Betreiber festlegt. Neben einer möglichst hohen Produktionsleistung kann das beispielsweise auch die Berücksichtigung von Kundenprioritäten sein. Diese Planungsebene wird als „Feinplanung“ bezeichnet, da sie die Grobplanung auf Tages- oder sogar Wochenebene aus dem Warenwirtschaftssystem auf eine feingranulare Linienbelegung pro Schicht detailliert. Maschinen- und Linienleistungen sowie der erforderliche Personalbedarf (einschließlich Mitarbeiterqualifikation) werden ebenso berücksichtigt wie verfügbare Lagerbestände und Rohstoffe.
„Irren ist menschlich“ und das kann auch dem motivierten und gut ausgebildeten Mitarbeiter jederzeit widerfahren. Personalfluktuation begünstigt diese Fehlerquelle natürlich nachhaltig. Deshalb ist es wichtig, dass das Fertigungsmanagementsystem (MES) den Werker eng führt und auf Anforderung erweiterte Hilfestellung gibt. Komplexe Fertigungsanweisungen werden bedienerfreundlich in Schritten aufbereitet und ggf. in verschiedenen Sprachen darstellt. Zudem sollten manuelle Prozessschritte durchgängig und umfassend dokumentiert werden. Dazu zählt auch der Einsatz von Barcode- bzw. QR-Code-Lesern, damit das MES Materialströme, Verpackungen, Lagerorte etc. konsequent nachvollziehen und überprüfen kann. Für wiederkehrend genutzte, mobile Transport- bzw. Lagerbehälter bietet sich auch der Einsatz von RFID-Tags (Transponder) an, die auch Produktionsdaten speichern können und die in robuster Umgebung (Reinigung) „überleben“.
„Digitale Assistenten“, die auf Algorithmen der Künstlichen Intelligenz (KI) basieren, können dem Bediener Vorschläge für eine optimale Einstellung von Linien- und Maschinenparametern unterbreiten. „Optimal“ bedeutet optimiert im Hinblick auf ein oder mehrere Gütekriterien, die der Anlagenbetreiber auswählen kann. Beispiele für solche Gütekriterien wären eine möglichst kurze Durchlaufzeit, minimaler Energieeinsatz, möglichst wenig Give-Away oder die Einhaltung eines Toleranzbandes für ein Qualitätsmerkmal des Produktes. Hierfür kommen als smarte Sensoren häufig Kamerasysteme (Machine Vision Systeme) mit einer Software zur KI-gestützten Bildverarbeitung zum Einsatz. Der Digitale Assistent muss angelernt werden und stellt dann seine erlernte Intelligenz beliebig vielen Linien bzw. Standorten 24/7 zur Verfügung.
Das Lager wird datentechnisch vom Warenwirtschaftssystem verwaltet. Die Produktionsprozesse können jedoch nicht durchgängig in das Warenwirtschaftssystem integriert werden, da Maschinenschnittstellen fehlen und die Produktionsabläufe das Warenwirtschaftssystem „nicht interessieren“. Diese „Lücke“ wird durch ein Fertigungsmanagementsystem (MES) vollständig ausgefüllt. Das MES kommuniziert mit dem Warenwirtschaftssystem, um Produktionsaufträge, Stücklisten (BOMs) und Chargeninformationen abzurufen sowie Gutmengen und Ausschuss am Ende der Produktionsprozesse zurückzumelden. Gleichzeitig kommuniziert das MES aber auch mit den Maschinen für Soll-/Istwerte, Störungen und Parametersätze sowie mit dem Werker zur angeleiteten und überwachten Ausführung manueller Arbeitsschritte.
Besonderes Augenmerk sollte auf die Festlegung der Chargenverfolgung zwischen Warenwirtschaft und MES bei der Bereitstellung der Rohstoffe gelegt werden. Wie definiert das Warenwirtschaftssystem den Lagerort und den Umfang einer Charge? Wird das MHD mitverwaltet? Wie soll das MES buchen? Und natürlich darf der Chargenbezug zum Warenwirtschaftssystem in der Produktion nicht verloren gehen.
Hier stellt sich zunächst die Frage, welche Prozesse besser definiert bzw. enger geführt werden sollten. Ggf. ist die Einführung weiterer QCP erforderlich. Das Fertigungsmanagementsystem (MES) hilft bei der Eingrenzung von Defiziten. Wann ist es wodurch zu einer konkreten Qualitätsstörung gekommen?
Methoden der „Statistical Process Control“ (SPC) helfen der Qualitätssicherung, relevante Prozesse frühzeitig zu identifizieren. Die Prozessfähigkeitsuntersuchung begleitet fortwährend die Produktion und erlaubt die Überwachung der Prozessfähigkeit und der Prozessstabilität. Entsprechende Sensoranbindung vorausgesetzt, kann die Datenerfassung automatisiert erfolgen.
Sobald die Ware verpackt ist, können Kameras oder Handscanner anhand von Barcodes / QR-Codes den Verbleib der Ware lückenlos verfolgen und dokumentieren. Die korrekte Etikettierung der Ware lässt sich mit Kamerasystemen (Machine Vision in Verbindung mit Künstlicher Intelligenz) absichern. Verifizierbar sind sowohl die Ausführung der Etikettierung wie auch die Gegenprüfung der gedruckten Informationen zu den Stammdaten des Fertigungsmanagementsystems (MES) für den speziellen Pack- oder Abfüllauftrag.
Die Schaffung von Transparenz ist ein zentrales Merkmal von Fertigungsmanagementsystemen (MES).
Logistische Herausforderungen ergeben sich sowohl bei der Steuerung von automatischen Förderstrecken wie auch von manuellen Transportvorgängen. Das MES übernimmt hier beispielsweise das Sortieren von Kartons, die Plausibilitätsprüfungen an Bereitstellungsorten und die Anzeige, welche Rohstoffe / Vorprodukte / Fertigwaren sich gerade an welchen Orten in der Produktion befinden. Die Erkennung von Kartons und Paletten erfolgt entweder automatisch mit Hilfe von QR-Code-Kameras oder manuell durch entsprechende Handscanner.
Gleiches gilt für Prozessbehälter, wie z. B. Mischer, deren Belegung mit Fertigungsaufträgen, Rohstoffen und Produkten jederzeit angezeigt wird.
Ein wichtiges Element der Prozesstransparenz ist es, Produktionsabläufe messbar und damit vergleichbar zu machen. Das Kennzahlenkonzept der „Overall Equipment Effectiveness“, kurz OEE, liefert hier einen wertvollen Ansatz. Die Stundenleistung an „Gut-Produkten“ wird mit der Verfügbarkeit der Maschinen / Linien in Beziehung gesetzt und zu einer Kennzahl verdichtet. So erkennen Sie auf einen Blick, wie effektiv gearbeitet wird, und das natürlich auch in der historischen Nachschau. Transparenz ist nicht nur für die Produktionsleitung wichtig, sondern motiviert auch den Bediener an den Maschinen bzw. Linien. Deshalb empfehlen wir, die OEE-Kennzahl auch an den Linien anzuzeigen. Zudem sollte der Linienführer im Falle von Ausfallzeiten (downtimes) die Gründe für den Stillstand am MES eintragen, da nicht alle Stillstandsgründe aus Informationen der SPS bzw. Maschine automatisch ermittelt werden können.
Grundsätzlich sind sämtliche, auch historische, Informationen aus dem Produktionsprozess in Echtzeit für jeden autorisierten Benutzer an jedem Arbeitsplatz verfügbar.
Gerade wenn ein geplanter Produktionsablauf durch unvorhergesehene Umstände kurzfristig angepasst wird, fällt es schwer, den Überblick zu behalten und sämtliche Folgen der Änderungen vollumfänglich abzusehen. Hier hilft das Werkzeug der Feinplanung, wie im Punkt „Es kommt zu unvorhergesehenen Änderungen in der Produktionsreihenfolge.“ beschrieben.
Jede Rückrufaktion ist mit einem enormen Schaden für die Marke verbunden. Deshalb ist ein stiller, begrenzter Rückruf immer noch die bessere Alternative im Vergleich zu einer öffentlichen Bekanntmachung, möglicherweise deutschland- oder europaweit („save the brand“). Eine zwingende Voraussetzung hierfür ist die konsequente, lückenlose Nachverfolgung der verarbeiteten Materialen (ggf. einschließlich Hilfsstoffe wie Verpackungsmaterial) über den gesamten Produktions- und Verpackungsprozess. „Tracking & Tracing“ ist deshalb eine Grundanforderung an jedes Fertigungsmanagementsystem (MES). Sobald Chargen vermischt werden, kann für die Rückverfolgung eine Konzentration für die Auflösung der Mischcharge gewählt werden. Ausgehend von der problematischen Eingangscharge werden alle Produktchargen, die einen Anteil größer oder gleich der gewählten Konzentration dieser Eingangscharge in % enthalten, ausgegeben.
Natürlich wäre es wünschenswert eine moderne Schnittstelle, beispielsweise auf Basis von OPC-UA und dem Weihenstephaner Standard oder dem PackML-Standard, an jeder Maschine zu implementieren, damit diese in das Informationsmanagement bzw. in die digitalisierten Prozesse eingebunden wird. Maschinenhersteller sind jedoch oft kaum in der Lage oder gewillt, eine solche Schnittstelle für Bestandsmaschinen anzubieten. Und wie integriert man ein Gerät, das gar nicht über eine SPS oder einen Microcontroller verfügt, aber für die Qualität bzw. Prozesssicherheit wichtig ist? „Alles neu!“ wäre sicher kein ökonomisch vertretbarer Ansatz. Hier ist die Praxisnähe des Fertigungsmanagementsystems (MES) gefordert. Auch proprietäre Maschinenschnittstellen müssen -wie vorhanden- integrationsfähig sein. Das Konzept einer „intelligenten Klemme“ erlaubt digitale und analoge Gerätesignale ohne eine dedizierte SPS direkt in das MES einzubinden. Solche Signale können unmittelbar an Schaltern, Hilfskontakten oder Sensoren abgegriffen, also nachverdrahtet werden. Dies erlaubt eine günstige und zuverlässige Digitalisierung von Bestandsgeräten.
Es ist eine Grundfunktion des MES, einen vielseitigen Schnittstellenmanager für die Vernetzung von Maschinen und Sensoren bereitzustellen.
Abgekündigte Bauteile (z. B. SPS-Komponenten, Kommunikationsbaugruppen oder proprietäre Controller), unsichere Unterstützung durch Maschinen- bzw. Anlagenlieferanten, veraltete Feldbussysteme und nicht mehr gewartete Softwareprodukte bzw. IT-Infrastruktur sind absehbare und damit vermeidbare Gründe für längere, ungeplante Produktionseinschränkungen oder Ausfälle. Konsequentes Handeln ist geboten. Dabei muss keineswegs eine teure Gesamtmodernisierung der Königsweg sein. Eine gemeinsame Begehung mit dem Ziel einer kritischen und gleichzeitig ökonomisch orientierten Bestandsanalyse ist das kurzfristige Mittel der Wahl. Aus der Notwendigkeit der Modernisierung ergibt sich zudem die Chance, einen nachhaltigen Digitalisierungsprozess anzustoßen.
Wir empfehlen, zusammen mit einem erfahrenen Berater das Gespräch mit den Fachabteilungen Produktion, Instandhaltung und Engineering zu suchen. Die Chancen, die sich aus einem solchen Vorgehen ergeben, sind immens. Lange Zeit praktizierte, oft sub-optimale Prozesse können erkannt und hinterfragt werden. Für die Integration der Produktion in die IT-Landschaft sollte zunächst aufgenommen werden, welche Möglichkeiten Prozesse und Maschinen heute schon bieten. Diese Möglichkeiten werden mit den erklärten Zielen der Digitalisierung in Verbindung gebracht. Hieraus resultiert ein sinnvoller Stufenplan mit Budgetabschätzungen für jede Ausbaustufe. Die möglichen Ziele sind vielfältig, sie finden sich üblicherweise in den Bereichen Qualitätssicherung, Betriebssicherheit, Transparenz, Flexibilität bzw. Produktionsplanung und Controlling. Ein wichtiges Element für das Controlling liegt darin, Produktionsabläufe messbar zu machen. Das Kennzahlenkonzept der „Overall Equipment Effectiveness“, kurz OEE, liefert hier einen wertvollen Ansatz. Die Stundenleistung an „Gut-Produkten“ wird mit der Verfügbarkeit der Maschinen / Linien in Beziehung gesetzt und zu einer Kennzahl verdichtet. So erkennen Sie auf einen Blick, wie effektiv gearbeitet wird, und das natürlich auch in der historischen Nachschau.
Das Fertigungsmanagementsystem (MES) unterstützt auch die Warenwirtschaft. Eine komplette Lagerverwaltung von Rohstoffen und Fertigwaren ist ebenso selbstverständlich wie der Einsatz von Betriebsaufträgen, die den bedarfsgerechten Warenausgang planen, indem Lagerware auf den Auftrag reserviert wird und für eventuelle Fehlmengen rechtzeitig die erforderliche Produktion geplant wird.
Bestände, Verbräuche und Produkte werden durchgängig und chargengenau gebucht.
Auch bei einer späteren Einführung eines Warenwirtschaftssystems behält das MES seine Daseinsberechtigung für die Anlagensteuerung und die konsequente Fortführung der Materialwirtschaft in der Produktion. Die Investitionssicherheit in ein solches System ist also gegeben.
Das MES verwaltet jedoch keine kommerziellen Vorgänge wie das Bestellwesen oder die Fakturierung.
Grundsätzlich sind sämtliche, auch historische, Informationen aus dem Produktionsprozess in Echtzeit für jeden autorisierten Benutzer an jedem Arbeitsplatz des Fertigungsmanagementsystems (MES) verfügbar. Spezifische produktionsnahe Reports werden mit einem Reportgenerator einmalig erstellt und sind dann auf beliebige historische Daten anwendbar.
Interne Audits lassen sich systemgestützt entweder ereignisorientiert oder zyklisch starten und der Verlauf dokumentieren. Sie sichern den Produktionsprozess nach der Methodik von HACCP und IFS ab.
Hier hilft die Personaleinsatzplanung eines Fertigungsmanagementsystems (MES). Mit der Feinplanung von Produktions- und Abfüllaufträgen / Verpackungsaufträgen kennt das MES für jede Linie, jede Maschine und jeden manuellen Arbeitsprozess den genauen Bedarf an erforderlichen Mitarbeitern einschließlich der benötigten Qualifikationen. Weitere Erläuterungen zum Planungssystem finden sie unter „Es kommt zu unvorhergesehenen Änderungen in der Produktionsreihenfolge.“
Sobald die Erfahrung eines Mitarbeiters wichtig für die bestmögliche Ausführung eines Prozessschrittes ist, sollte der Einsatz von Künstlicher Intelligenz (KI) in Betracht gezogen werden. Das optimale Einstellen von Maschinenparametern -auch in ganzen Produktionslinien- ist ein Thema, sobald klassische Methoden der Regelungstechnik wegen der Vielzahl der sich gegenseitig beeinflussenden Parameter oder wegen langer Totzeiten im Fertigungsprozess nicht mehr zum Tragen kommen. Auch die Klassifizierung eines Produktes oder Rohstoffes an einem QCP kann durch ein KI-basiertes System zuverlässig, reproduzierbar und ohne Beteiligung eines Mitarbeiters durchgeführt werden. Neben Machine-Vision-Systemen, die Methoden der Bilderkennung nutzen, stellt auch eine Kombination der Messwerte aus Hard- und Softsensoren eine sinnvolle Eingangsgröße für KI-Algorithmen zur Verfügung.
Wenn Sie einer oder mehrerer dieser Aussagen zustimmen, dann sollten wir uns zum Thema digitale Transformation unterhalten.
Wie ist das typische Vorgehen, falls das Erstgespräch interessante Ansätze für eine Digitalisierungsstrategie liefert?
Zunächst werden in einem gemeinsamen Workshop die Ist-Prozesse aufgenommen und dokumentiert. Gemeinsam werden Potenziale von digitalen Lösungen in Ihrem Produktionsumfeld ermittelt.
Wir erstellen daraufhin in enger Absprache ein Grobkonzept für den Einsatz von Tools aus dem Manufacturing Operations Management. Dieses Grobkonzept beinhaltet in der Regel auch einen Ausblick auf den stufenweisen Ausbau des Grundkonzeptes. Eine erste Budgetschätzung ist ebenfalls Bestandteil des Konzeptvorschlages.
Aktuelle Schlagworte wie „IoT“, „Digitaler Zwilling“, „Big Data“ oder „Künstliche Intelligenz“ entmystifizieren wir im Rahmen eines solchen Workshops und zeigen die Chancen, aber auch die Grenzen einer digitalen Produktion für Ihren Anwendungsfall auf.
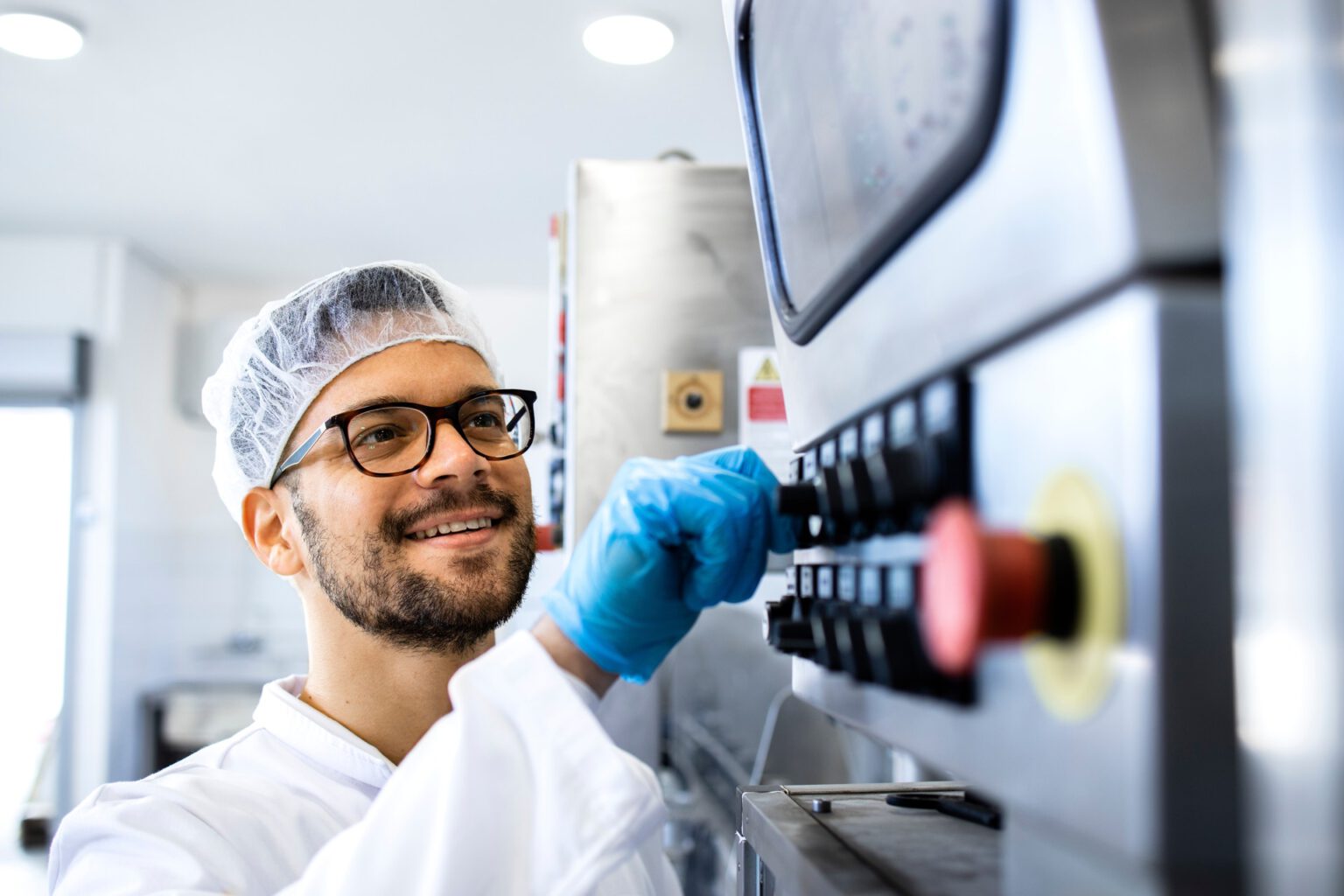
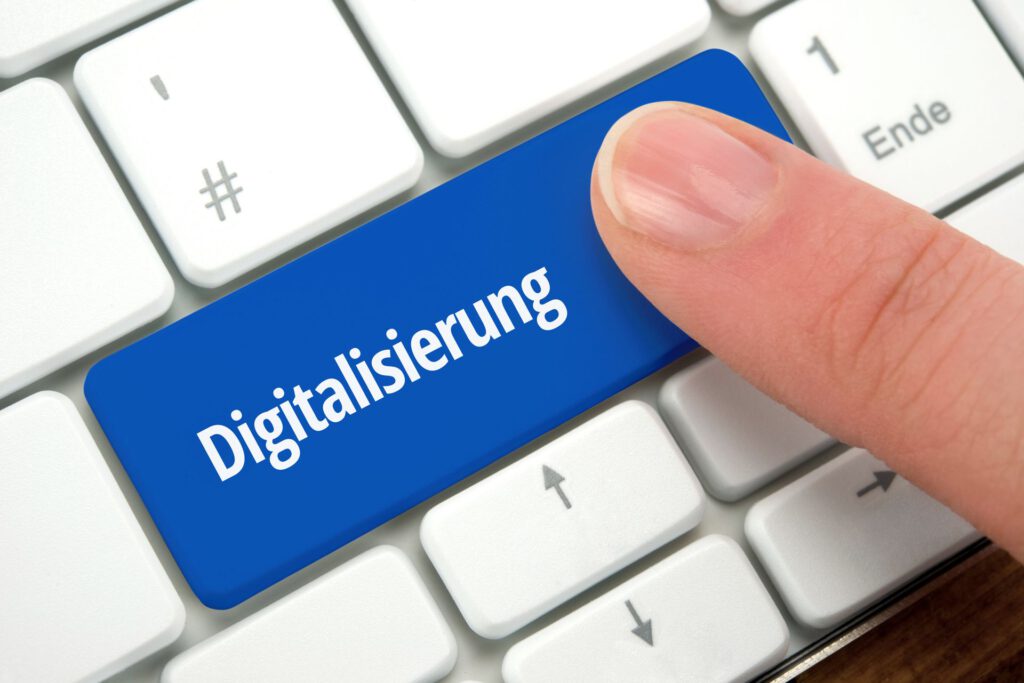
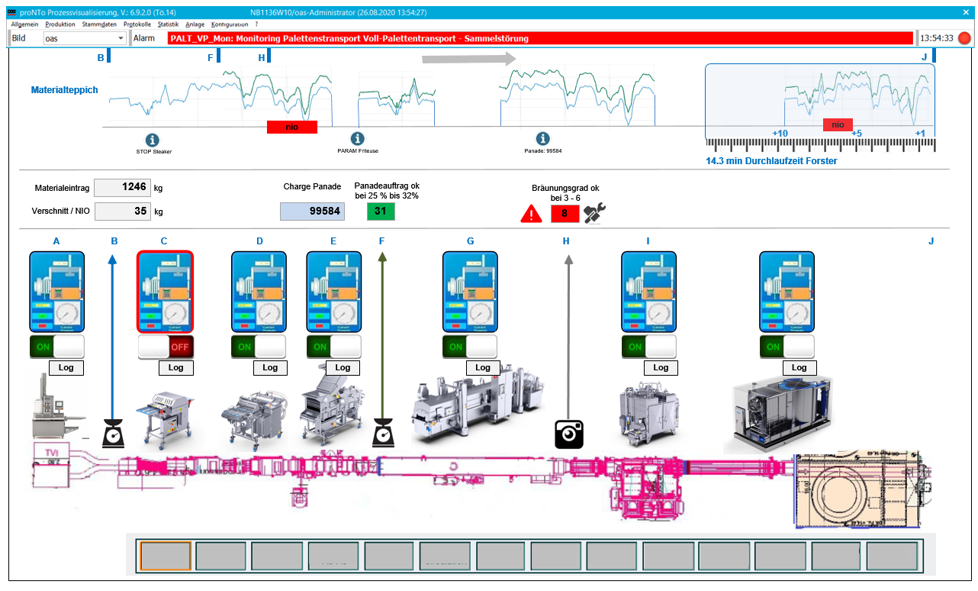